Koenigsegg preparing its cars for crash tests is an ugly affair
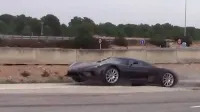
As company homologation manager David Tugas explains, Koenigsegg can’t simply pull a dozen cars off a production line for crash testing. The carbon monocoque that forms the passenger cell is the crucial structure; everything else is expendable. A supercomputer in the company basement runs simulations on how carbon fiber structures behave in crashes, helping the company design a monocoque that can withstand the necessary impacts. So unless the monocoque breaks, the same passenger cell gets used in all the crash tests. After that, it’s cheaper for Koenigsegg to simply rebuild the body panels and mechanical parts attached to the monocoque that break during in-house testing. It’s all rather Formula 1.
It takes three months to prepare a crash test car for testing at a facility in Barcelona. That will cover everything from getting the smart airbags to blow in just the right way with just the right force, to getting them not to blow when someone hits the undercarriage with a sledgehammer. The knowledge and the carnage help explain where the $2 or $3 million goes in ever Koenigsegg.